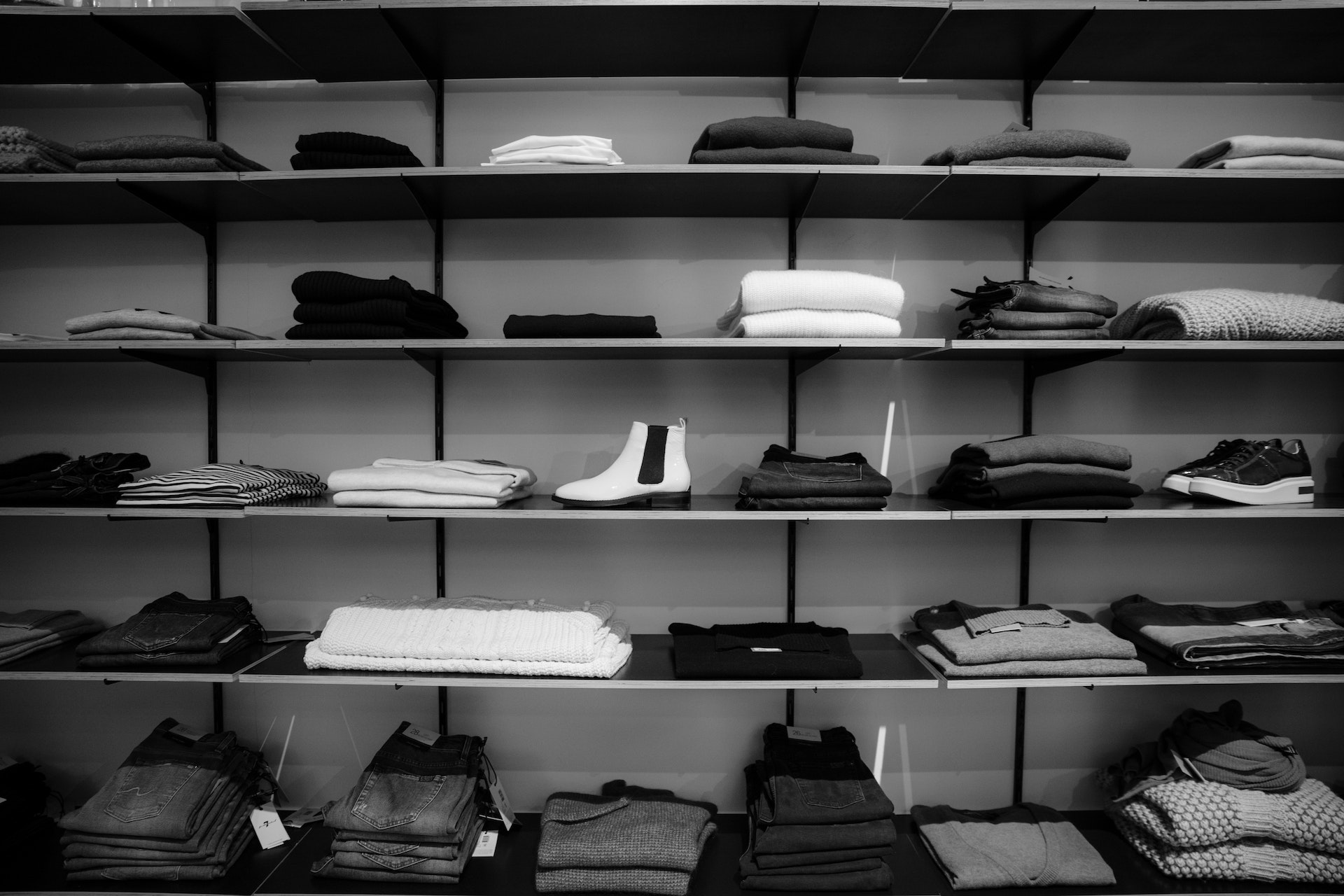
Screen printing transfers for shirts is a fun and easy way to add personalized touches to your wardrobe. It’s an excellent project for beginners and those looking for a creative outlet. With the right tools and some basic instructions, you can create beautiful shirts with vibrant designs.
First, you’ll need to acquire the materials and supplies to make screen printing transfers. You’ll need t-shirts, screen printing transfer papers, a cutting/plotting machine, iron-on transfer paper, printed iron-on vinyl sheets, craft heat press machine, screen printing emulsions or sensitizing chemistries, soy-based ink transfers and light source. Once you have all of your materials assembled, you can begin.
Next up is creating your artwork. Using the software program of your choice (Adobe Illustrator is one popular option), create a digital image that has been flipped both horizontally and vertically from the original image. This will ensure that when printed by an iron-on transfer machine it will appear as it should on the shirt. Once you have your artwork prepared in the digital format of choice (JPEG or PNG works best) send it over to be transferred onto your t-shirt with the machine of choice.
Lastly, you will need to “cure” or “fix” the ink so that it does not come off in the washer or dryer after a few wears. To do this use either an emulsion or sensitizing agent designed for screen printing on fabric followed by curing in a heat press at 350°F - 400°F for 20 seconds with medium pressure applied evenly throughout. And voila there you have it! Congratulations on successfully engineering a custom one-of-a-kind design on your garment!
By following these steps you now know how to make beautiful screen print transfers for t-shirts quickly and easily - providing endless possibilities for expressing yourself through design! Will you try out screen printing? If so what type of print are you inspired to create?
What materials are required for creating screen print transfers for T-shirts?
Creating a DIY screen print transfer for a t-shirt is an easy and unique way to express creativity. To successfully create a quality image on a t-shirt, one must have the right materials beforehand. The three main ingredients needed are a silkscreen, ink, and paper.
First is the silkscreen: this can be purchased from any craft store, but most importantly it should have an opening specifically for the design you would like to print on your t-shirt. An important tip when purchasing one – Its important to use a fabric-specific ink with most silkscreens as opposed to typical inks you may find at online stores or art stores.
Second is the ink: there are both oil and water based formulas of screen printing inks available - make sure not to mix the two types together as they will not work properly. Each type of ink will give your design different characteristics like colour vibrancy or opacity; it’s up to what you prefer that determines the better use of ink for your design!
Lastly, quality paper: since heat needs to be applied during the process of printing on your t-shirt, it is important for you to choose some quality material that won't burn easily.This could include either parchment paper or even wax-based paper if you're looking for something more durable. The thickness of the actual paper should also be kept in mind prior to buying; it’s ideal that your chosen paper is at least 10pt thick which ensures your design won't be damaged when receiving heat application.
By gathering all these essential materials, you’ll be ready to start crafting fun designs onto any type of t-shirt! Enjoy expressing yourself whilst keeping yours creative juices flowing.
Readers also liked: Does Not Play Well with Others T Shirt?
What method is used to apply screen print transfers to garments?
Screen printing transfers are a great way to add artwork, designs, and text to your favorite garments without having to order large numbers of custom-made items. The process of applying screen print transfers is relatively simple, but requires some specialized tools and techniques.
First, the graphic or design must be printed onto transfer paper. This paper has a coating that allows the image from the printer to adhere to it after printing. Once printed, the transfer paper with the design is placed next to the garment in an appropriate position and secured with heat resistant tape. Some screen printers will then trim any excess material around the edges of the transfer paper before application.
The second step involves raising the temperature of either the object being printed or the substrate it is being placed onto. Raising this temperature will help ensure an even coat of ink across your designs or graphics. Heat press machines are typically used for this stage of screen printing transfers; however, other methods including irons can also be utilized. After heating, flipping the garment and heated transfer paper over so that the design facing away from you will result in better output results when placing down pressure on top.
Once reversed and secure with pressure applied across them both for a short period of time, gently peeling away both layers reveals an evenly thick layer of ink across your desired artwork on your garment!
For another approach, see: Sublimation Paper
How long does it take to create a screen print transfer for a T-shirt?
Creating your own screen print transfer for a T-shirt is a great way to have a unique and personalized look to your wardrobe. Whether you’re a fashion designer, an artist looking for a wearable canvas for their work, or an individual wanting to stand out with custom-made, one-of-a-kind apparel, the process of creating your own screen print transfer can be incredibly satisfying.
The first step in creating a screen print transfer is to design and draw the desired image onto paper. Using photosensitive transfer paper, the design is then copied onto the paper. Depending on the degree of complexity of your image, this step can take anywhere from several minutes to over an hour. After this step has been completed, it is time to apply it to the shirt itself using specialized inkjet fabric sheets. As long as you have good and evenly dispersed layers that cover every corner of your fabric, you should be able to get a seamless effect that comes out looking great. This entire process usually takes about 30 minutes or so depending on how skilled you are with placing and positioning textile transfers on clothing materials.
Finally, once everything has been printed on perfectly and allowed plenty of time for drying and curing, you can start wearing or selling your finished product proudly. All in all, depending on how complex your design is and how long it takes you type up the proper transfer documents - creating a professional looking screen print shirt should take no longer than one or two hours maximum.
What is the best way to design a screen print transfer for a T-shirt?
Creating a beautiful and eye-catching screen print transfer for a T-shirt is a great way to enhance your artistic vision and reach! However, it can also be daunting for beginners if you don’t know where to start in order to create the desired effect.
The best way to design your screen print transfer is to use an image manipulation program, such as Adobe Photoshop, Inkscape, or even Gimp. This will allow you to easily envision the end product and make all necessary alterations. After you find your desired image, it’s important to plan out the sizing correctly. It should be large enough that the details of the design can be seen in proporation when printed on the shirt. If utilizing text styled designs, choose fonts which compliment each other but aren’t too elaborate so they are still legible when printed.
Transparency plays an important role as well when it comes to T-shirt transfers, as it enhances contrast and prevents any background patterns from showing through your design. Ground yourself in research on printing specifics like CMYK color mode and file types such as.tif and.eps; understanding these basics gives better control over how your images come out after printing them on a T-shirt. At this point you are ready to send your transfer design file off for processing; once finished applying with a commercial heat press using special pressure settings (at least 350°F) ensures their longevity!
Through following these steps one can easily create quality screen print transfers for customizing T-shirts without hassle!
What type of printer is necessary for printing out a screen print transfer for a T-shirt?
In the modern era, printing one-off clothing items such as T-shirts is growing in popularity. It allows for increased creativity, affordability and unlimited potential for unique designs that can’t easily be found in local stores. But to begin this journey of textile design and print, you will need the right tools.
At the core of investment will be the right type of printer – with a real emphasis on selecting one that is both compatible with and capable of producing screen transfer prints. Specifically, an inkjet printer with pigment-reactive inks is best suited towards this task due to their quick drying properties, which are often a prerequisite for garment printing. It should also have a high resolution print setting of at least 1440x720 dots per inch (dpi), support for high yield cartridges, and roll paper support for larger tasks.
Maintenance costs should also play a part in your purchasing decision; some brands tend to relegate certain parts only to either manufacturer repairs or require additional third-party purchases to keep them working correctly over time. Research into refillable ink systems could offer significant savings over time as well as being kinder to the environment when compared to standard inks supplied by manufacturers.
Overall, selecting an appropriate printer when deciding on screen transfer prints can limit unnecessary setbacks while improving quality output - making it easier than ever to see your prints become reality quickly and with great precision.
For another approach, see: Dry Screen Printed Shirts
Are there any available tutorials for creating a screen print transfers for a shirt?
Creating your own custom shirts through screen print transfers can be a great way to express your personal style and to create unique, one-of-a-kind wardrobe pieces. As it may seem like a daunting task, the nice thing is there are plenty of tutorials available online that will help you understand and complete the job.
When working to create your own screen print transfer, the first thing you want to do is gather up all the necessary supplies and materials. This includes fabric markers or paint in the color of your choosing, some kind of clear coat sealant such as polymer fixative, paper and cardboard for printing perfect copies of your designs on sheets with ink resistant surfaces. After gathering up all these supplies, you’ll need blank t-shirts for you printed designs to be transferred onto.
Once all those pieces are in place, the next step is designing your transfer and uploading it into a computer program to prepare it for print. From there, use a laserjet printer or an inkjet printer with pigmented inks that have been specifically formulated for printing onto specialty media such as laser transparencies or T-shirt transfers. After printing them out onto parchmenting paper or another media that’s specially made for utilizing transfer strategies, apply them face down on the shirts using heat from either an iron or other heated media press method while providing pressure ensuring they stay in place during the process. Once it cools down again, peel off carefully and voila!
Overall, creating custom shirt designs through screen print transfers doesn’t have to be as intimidating as it may initially seem! While some may feel more comfortable seeking professional services when needed - this should prove how easy it is if you were to try it yourself! Plus tutorials give not only insight into how this can be done but also an understanding why they had success achieving these results!
Readers also liked: Custom Vinyl Shirts
Sources
- https://www.printtopeer.com/make-screen-print-transfers/
- https://www.transferexpress.com/heat-applied-transfers/screen-printed-transfers
- https://printbindship.com/screen-print-tshirts/
- https://www.wikihow.com/Screen-Print-a-T-Shirt
- https://www.merchology.com/pages/custom-decoration-methods
- https://doitsomething.com/screen-print-transfer-printer/
- https://www.printtopeer.com/t-shirt-printing-materials-list/
- https://www.transferexpress.com/videos/creating-custom-screen-printed-shirt-tags
- https://proactivecreative.com/best-printer-for-screen-printing/
- https://www.yoprint.com/a-quick-guide-to-screen-printed-transfers/
- https://whiskeyandwhit.com/how-to-screen-print-shirts-and-decor-with-your-cricut-step-by-step-video-tutorial/
- https://tshirtplus.com.au/blog/screen-print-guide/
- https://www.parkwayprintshop.com/blog/screen-printing-vs-transfers
- https://www.jupmode.com/blogs/news/heat-transfer-vs-screen-printing-for-t-shirts-buyers-guide
- https://www.tshirtriches.com/screen-print-transfers/
Featured Images: pexels.com